Round Tabletop and Base
ONE: TABLE BASE FORMING
Video Overview
See how the form for this outdoor table base is created. The base will have 3/4-inch thick walls and be 27 inches tall. The mold is complicated because of the curve of the base. A CAD file is sent to a foam fabricator who makes the mold with a CNC machine and coats it in epoxy resin
Step 1 – Design Details
Step 2 – Foam and Epoxy Mold
Next: Table Base Spraying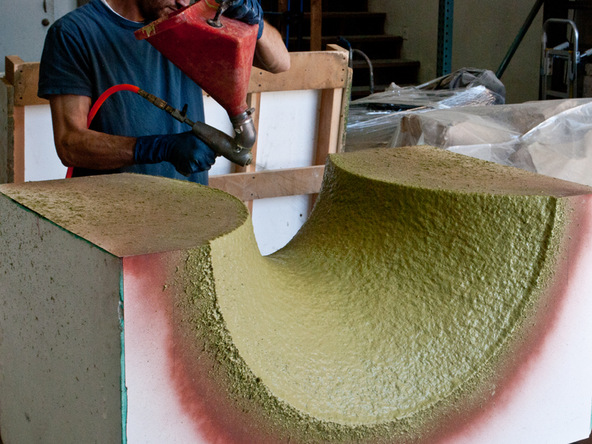
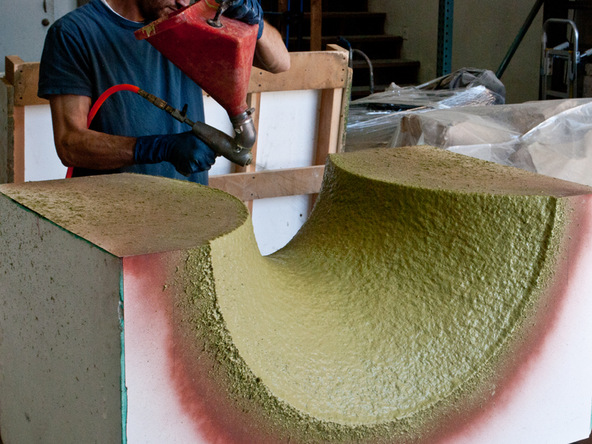
Each half of the form is initially cast separately to allow efficient placement of the fiber reinforced concrete mix before the forms are seamed together.