Recycled Glass Countertops
SIX: POLISHING
Polishing your recycled glass countertop will take a considerable amount of time and patience. The glass aggregate is very hard and we need to remove a lot of material to expose the glass and create a homogenous appearance.
For this project we chose to use a single head wet/dry polisher, but if this project were any bigger, we’d have used a triple-head planetary polisher for faster results.
Use the lithium densifier while polishing to create a slurry to fill in air pockets as you go. This method creates a slurry that closely resembles the base mix, but if you prefer using conventional acrylic slurry, that option is always available.
What You’ll Need
Step 1 – Polish your Countertop
Step 2 – Create Slurry
Step 3 – Continue Polishing
Step 4 – Before/After
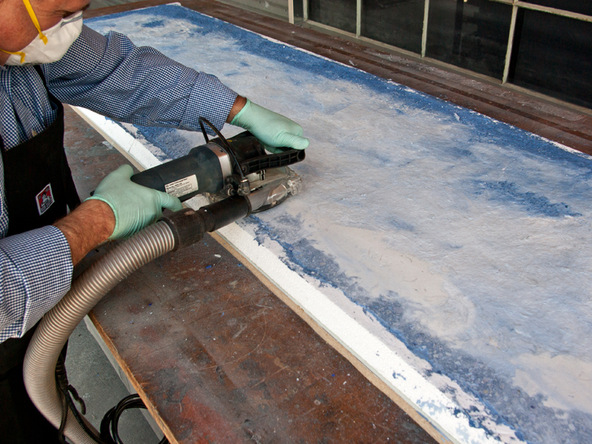
Use a grinder to level any high spots or aggregate that protrude above the form walls. This is also when we ease the sharp edges along the underside.
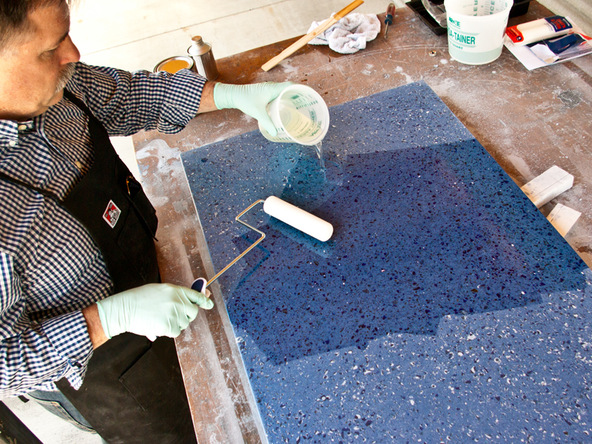
To achieve the boldest color possible, we sealed this recycled glass countertop section with a high-gloss color-enhancing sealer from Surecrete.