Recycled Glass Countertops
TWO: FORMING
This is a basic 3/4″ countertop slab that requires very little effort to form. Using a simple foam rail and adhesive forming system, we were able to build this entire countertop mold in less than 1 hour. The most time consuming part of this process was sealing the mold with silicone sealant.
What You’ll Need
- Chop Saw/Table Saw
- Utility Knife
- Vibco Table Vibrator
- Vibco Variable Speed Controller
- 3M Super 77 Spray Adhesive
- Straight Edge
- Scissors
- Level
- 3/4″ Melamine
- Caulking Gun
- 100% Silicone Caulk
- Corner and Seam Shaping Tools
- Concrete Countertop Forms
- Double-Sided Carpet Tape
Step 1 – Lay Out on Melamine Form Base
Step 2 – Cutting Form Walls to the Correct Height
Step 3 – Attach Form Walls to Form Base
Step 4 – Cut Wall Liners
Step 5 – Glue Wall Liners to Form Walls
Step 6 – Seal the Form
Step 7 – Level Form
Step 8 – Attach Vibrator to Casting Table
Previous: Support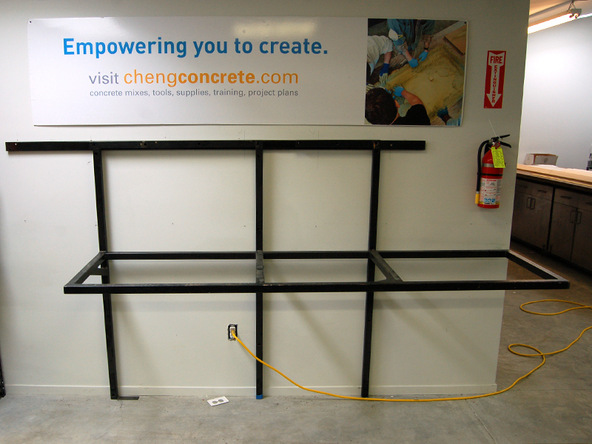
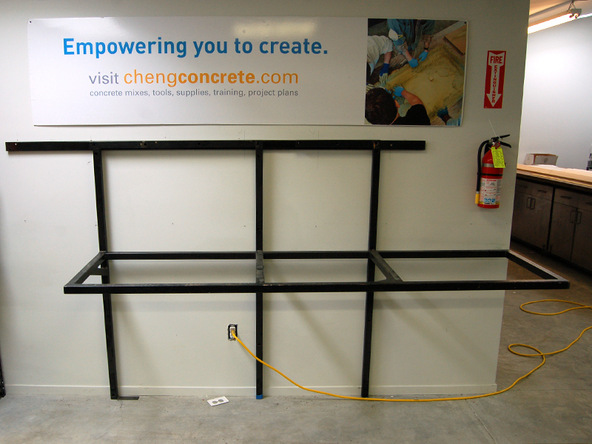
Here are a few basic rules to consider. The support must be flat, level, stable, securely anchored, and strong enough to support a heavy load.
Next: Mixing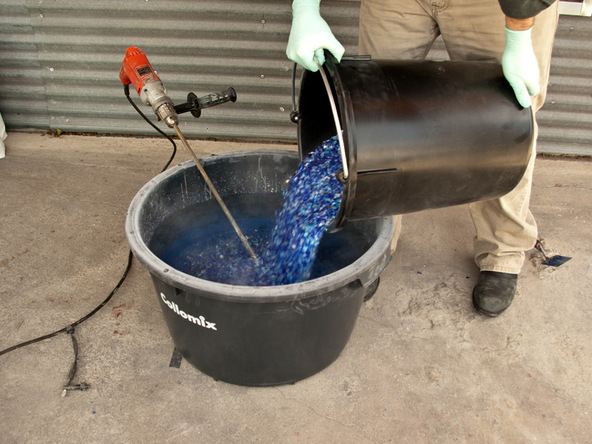
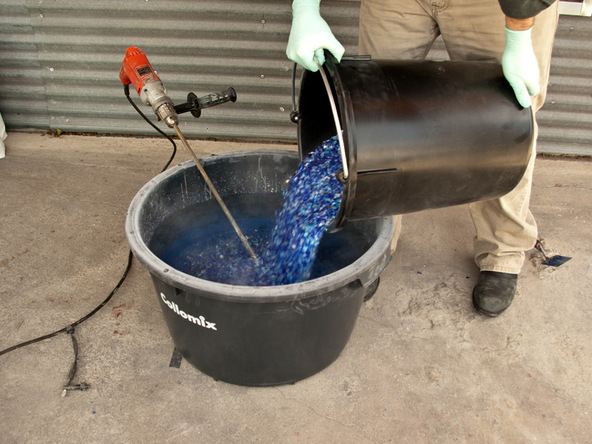
No need for a large drum style concrete mixer for this project. A 1/2″ drill motor, equipped with a good paddle mixer, is all that’s required.