Precast Concrete Countertops
TWO: BUILD THE MOLD
There are many different mold methods to choose from when planning your concrete countertop. Everything from plywood to plexiglas and sheet metal to fabric have been used for good reason.
In this guide we’ll introduce you to the most common concrete countertop forming method – melamine-coated particle board. It’s inexpensive, readily available and most importantly… it’s pre-sealed!
The plastic coating makes an ideal casting surface for projects which are destined for the polishing process. Once the countertop is removed from the mold, there will be a subtle “orange peel” texture to the concrete which is removed with the quick action of a wet-polisher and diamond polishing pads.
What You’ll Need
- Table Saw
- Cordless Drill
- Pilot and Countersink Bit
- Phillips Driver Bit
- Drywall Screws (1-5/8″)
- 100% Silicone Window and Door Sealant
- Razor Blades
- CHENG Corner and Seam Shaping Tools
- 3M Super 77 Spray Adhesive
- Caulking Gun
- 3/4″ Melamine-Coated Particle Board
- Insulating Foam
- Glossy Form Tape
- Faucet Forms
- Concrete Countertop Forms
Step 1 – Getting Started
Step 2 – The Sink Knock-Out
Step 3 – Cutting Board Recess
Step 4 – Sink Notes
Step 5 – Plumbing Penetrations
Step 6 – Seal the Mold
Step 7 – Decorative Aggregates
Step 8 – Reinforcement
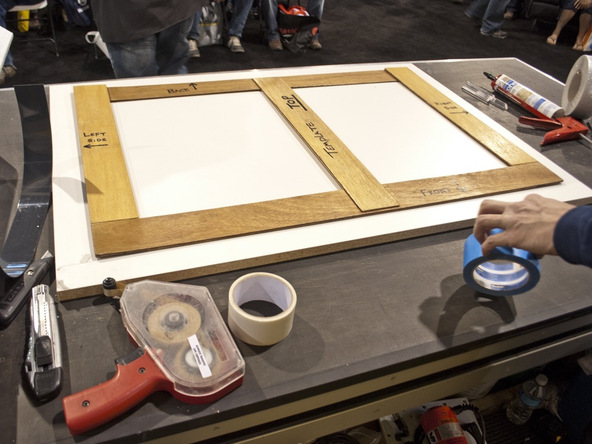
Every countertop project begins with an accurate template. Detailed notations, measurements, and planning will help your project flow as smoothly as possible.
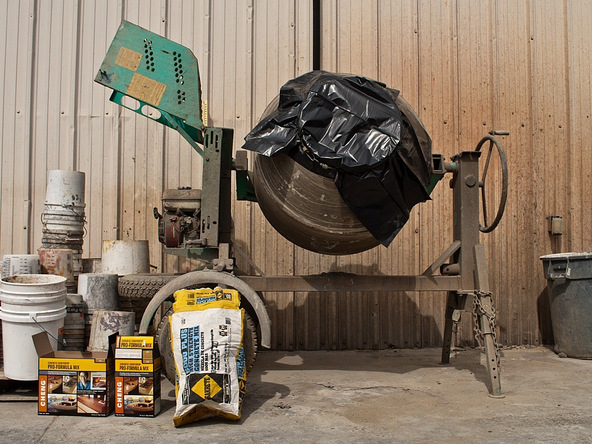
Keep your costs low with Sakrete 5000 Plus concrete from your local home improvement center, and CHENG Pro-Formula Concrete Countertop Mix.