Round Tabletop and Base
THREE: TABLE BASE CASTING
What You’ll Need
Watch how the two mold haves are assembled and a layer of casting blend is sprayed into the mold. Plus see how the seams are reinforced with fiberglass scrims. Around 120 pounds of concrete go into this table base.
Step 1 – Hand Lay Up
Previous: Table Base Spraying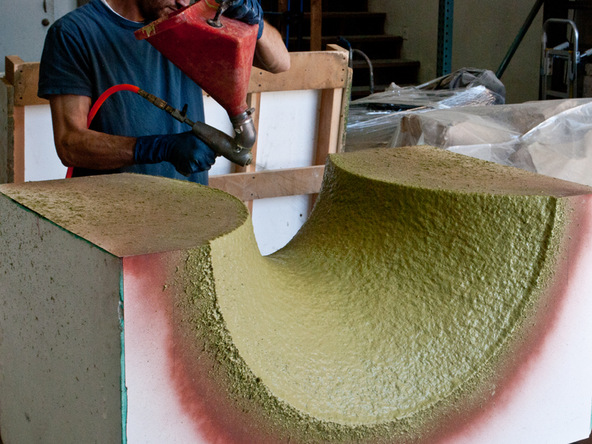
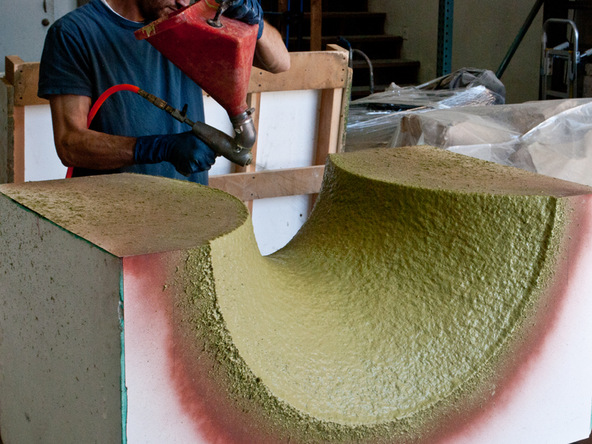
Each half of the form is initially cast separately to allow efficient placement of the fiber reinforced concrete mix before the forms are seamed together.
Next: Tabletop Forming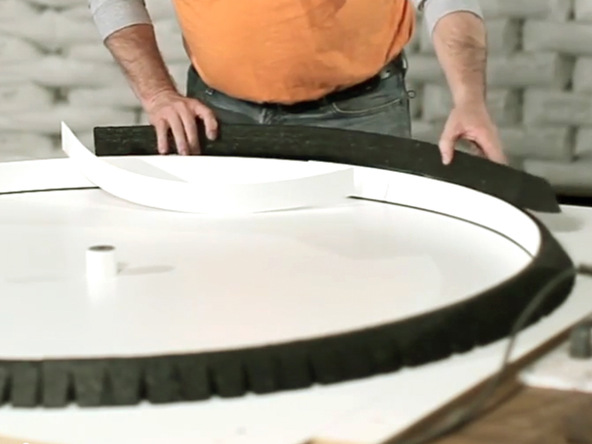
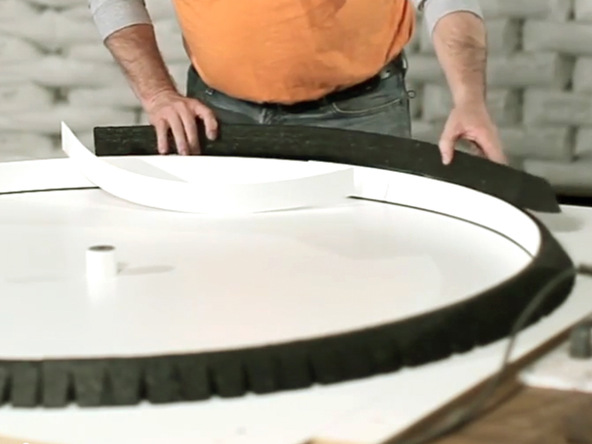
3/4″ melamine and EPS foam are used to shape this 48″ diameter table top. The table also has a hole in the middle to accommodate a large table umbrella.